5 Types of Mold Classifications
Which Class Is Right for Your Project?
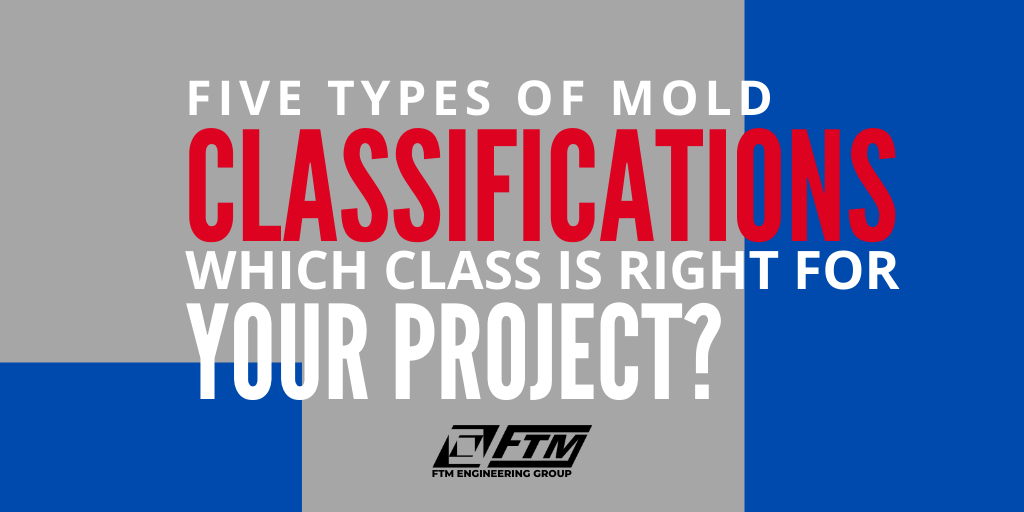
Mold Classifications: Which Class is Right for Your Project?
Have you ever received quotes from different custom injection molders that were so far apart, you seriously wondered if they were actually quoting the same project?
Us, too. We’ve been on the quoting end and have questioned the same thing.
When evaluating and quoting a custom plastic injection molding project, it’s important to consider more than just the basic specifications of the project. If a potential vendor is not fully educated in the standards of mold classifications, that company may be presenting a quote that - while it may seem on spec at a glance - is actually nowhere near the quality you’re looking for.
Standard molds are defined by the Plastics Industry Association (PIA, formerly known as the Society of Plastics Industry or SPI). These mold standards are categorized into five classifications to guide quotes and orders into uniform mold types: (click image to enlarge)
While these guidelines are intended to be used as a reference point that is continually evolving, they offer a simplified definition of the type of thermoplastics required for a set production need. This allows for comparing “apples to apples” in the area of custom mold designs.
Class 101 Mold/Tool
Cycles: One million or more
Quality: High
Price: High
Uses: High quality production and fast cycle times
Class 102 Mold/Tool
Cycles: Not exceeding one million
Quality: Medium to High
Price: Fairly High
Uses: Parts with tight tolerances and/or abrasive materials
Class 103 Mold/Tool
Cycles: Not exceeding 500,000
Quality: Medium
Price: Mid-range
Uses: Low to medium production parts
Class 104 Mold/Tool
Cycles: Not exceeding 100,000
Quality: Low
Price: Low to mid-range
Uses: Limited production of non-abrasive parts
Class 105 Mold/Tool
Cycles: Not exceeding 500
Quality: Very low
Price: Low to accommodate limited number produced
Uses: Prototypes
Every custom plastic injection molded part has its own unique parameters, and you should consider more than a quick review of these mold classifications. Budget, quality and desired production life are all essential pieces of information that should be discussed with whoever you’re working with to build your mold/tool.
There are benefits to a one-stop shop.
In most cases, there are custom tooling/mold builders and those who actually use those tools to produce/manufacture these custom injection molded parts. When you find a partner who has the knowledge and expertise to do both, it can seem too good to be true.
At FTM Engineering Group, we have the unique combination of capabilities that allow us to both design and build the tooling, as well as manufacture the custom plastic injection molded parts that those tools are made to produce.
Are you working on a project right now and have questions?
Let’s start by having a quick conversation. You can contact us today or go ahead and formally request a quote.