Seven Possible Reasons Your Precision Parts are Out of Tolerance (Part 1)
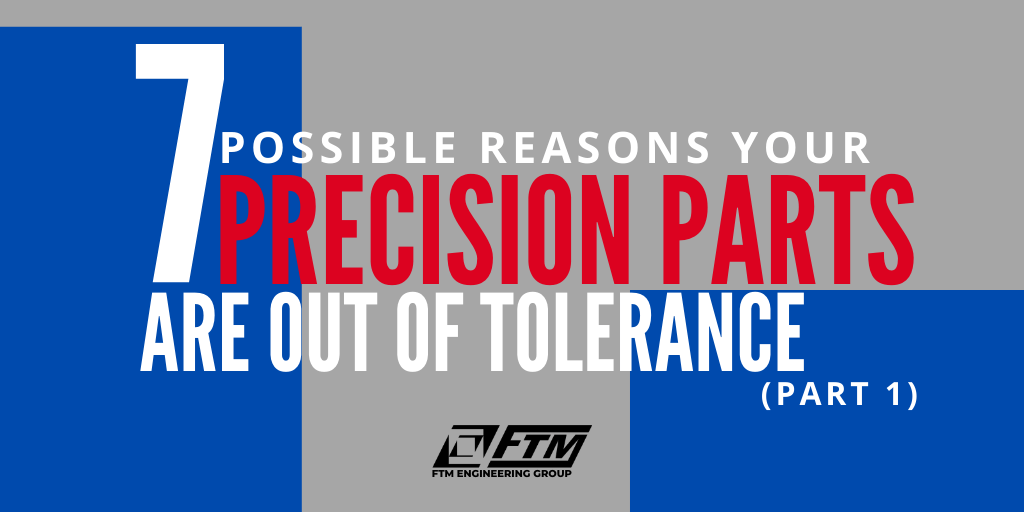
Seven Possible Reasons Your Precision Parts are Out of Tolerance (Part 1)
There’s almost nothing more frustrating than a part that’s out of tolerance.
You and your plastic injection mold partner spent weeks - maybe months - designing, engineering and building a mold that was intended to produce close tolerance parts that are made exactly to spec. That’s why they’re called “close tolerance” parts!
Whether you just started using the mold or slight tolerance variations have begun to show up over time, we have seven possible reasons your precision parts are out of tolerance. Some may be able to be fixed by making a few small adjustments, while others will cause you to look back at the original design and engineering of the mold and may require a complete rebuild.
1. Material Shrink Rates - the quality of an injection molded part’s geometry, performance, and appearance can often have a direct correlation to the shrink rate of a particular material.
Different shrink rates - different materials have different shrink rates, and these rates should be considered when designing and engineering the mold.
Material moisture content - moisture within and outside of the material can cause abnormal shrinkage; something as simple as the temperature in the room can actually create an increase or decrease in shrink rates.
Placement of the gate - it is important to have gate locations that provide the most uniform fill and plastic pressure within the cavity.
In-flow and cross-flow - flow direction can affect material shrink rates; it’s important to carefully analyze both in-flow and cross-flow after gate selection has been made.
Steel safe - depending on the mold design, there is often a need for “extra” steel to be included in the design to accommodate possible shrink rate changes.
Anticipate possible adjustments - an experienced mold builder will anticipate many of these potential changes and adjust the design accordingly from the very beginning.
2. Injection Molding Process - with so many steps in the injection molding process, there are a variety of areas where issues can arise that may cause a part to be out of tolerance.
Pressure - too much or too little pressure in the injection molding process can make all the difference in the precise tolerance of a plastic part.
Temperatures - it’s important to maintain the ideal temperature of both the mold itself and the plastic material being used.
Fill speed - minor adjustments in the fill speed can make an impact on the finished product.
Amount of regrind - there are benefits to utilizing regrind effectively and efficiently, but the amount of regrind used can have an impact on the final specs of a part.
Degraded material - the quality and consistency of the material used in an injection molding process will have a direct impact on a finished product.
People - we all like to think we have properly trained the people working on an injection molding machine, but it can cause trouble if that is taken for granted.
Machine issues - sometimes a machine has problems that go unresolved and over time those problems ultimately create a major breakdown in the process.
Bad preventative maintenance - without proper preventative maintenance, any injection molding process will have problems and cause parts to be out of tolerance.
3. Imbalanced Gates/Hot Runner Systems - many part defects are caused by flow imbalance; ensuring a balance in the gates and runners is vital to producing a consistent, precise part.
Gate size variations - when the gates have even the slightest variation in size, this can create inconsistency from cavity to cavity.
Gate worn out - over time, gates can simply wear down causing a degradation of the resulting final product.
Runner imbalance - melt homogeneity and the consistency in which the hot runner gates open can affect the precision needed for a close tolerance part.
Temperature control - when temperatures are inconsistent the flow of the resin throughout the mold can be adversely affected.
If you are struggling to maintain consistency in the production of your close tolerance parts, it could be related to one of the issues above. We would love to talk through these possible problems with you and see if there’s some way we can help.
We will be addressing another four possible reasons your parts are out of tolerance in Part 2 of this blog post, including: (click here to read Part 2)
Improper venting
Worn or corroded components
Insufficient cooling
Inconsistent wall thickness
Are you working on a project right now and have questions?
Let’s start by having a quick conversation. You can contact us today or go ahead and formally request a quote.